|
ACCESS THE FULL ARTICLE
No SPIE Account? Create one
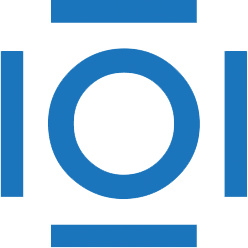
CITATIONS
Cited by 1 scholarly publication and 1 patent.
Image processing
Image quality
Optical proximity correction
Semiconducting wafers
Etching
Metals
Resolution enhancement technologies