|
ACCESS THE FULL ARTICLE
No SPIE Account? Create one
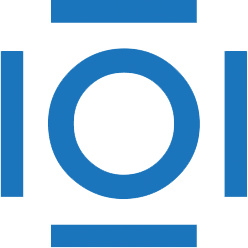
CITATIONS
Cited by 8 scholarly publications.
Polishing
Surface finishing
Magnetorheological finishing
Applied sciences
Photovoltaics
Process control
Data conversion