|
ACCESS THE FULL ARTICLE
No SPIE Account? Create one
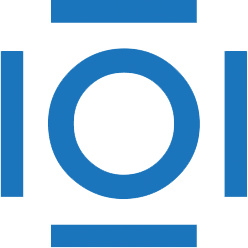
CITATIONS
Cited by 6 scholarly publications.
Optical proximity correction
Tolerancing
Information technology
Data modeling
Resolution enhancement technologies
Image quality standards
Optimization (mathematics)