|
ACCESS THE FULL ARTICLE
No SPIE Account? Create one
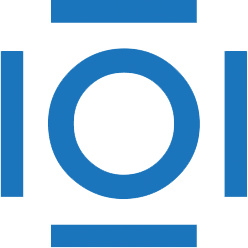
CITATIONS
Cited by 7 scholarly publications.
Etching
Semiconducting wafers
Photomasks
Silicon
Charged-particle lithography
Helium
Plasma etching