|
ACCESS THE FULL ARTICLE
No SPIE Account? Create one
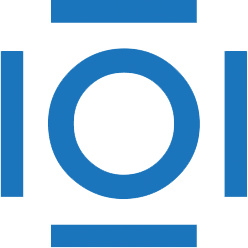
CITATIONS
Cited by 26 scholarly publications and 1 patent.
Actuators
Shape memory alloys
Ceramics
Smart materials
Aerodynamics
Control systems
Electrodes