|
ACCESS THE FULL ARTICLE
No SPIE Account? Create one
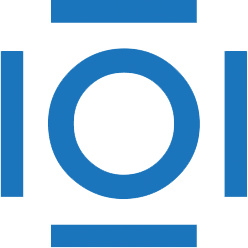
CITATIONS
Cited by 3 scholarly publications.
Etching
Reflectivity
Antireflective coatings
Lithography
Deep ultraviolet
Photoresist materials
Semiconducting wafers